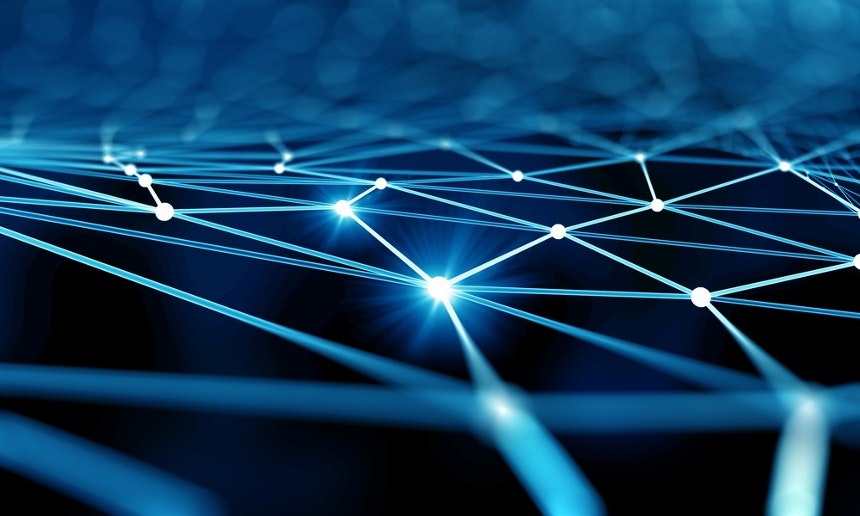
The fourth industrial revolution is here. The first three industrial revolutions respectively brought mechanization, mass production, and digital technologies to manufacturing – but the fourth revolution is going a step further with the introduction of truly autonomous, connected machines. With the advances in human-machine interfaces, and the proliferation of cloud computing, the internet of things (IoT) and the industrial internet of things (IIoT), Manufacturing 4.0 is in full swing.
Through unprecedented machine interconnectivity, these new technologies are taking factory automation to an entirely new level. IoT sensors collect vast quantities of information across networks of machines and devices, and that data drives automated decision-making – paving the way for truly smart factories.
The benefits of Industry 4.0 are clear. Automation naturally leads to increased productivity and reduced time-to-market; and IoT solutions can empower manufacturers to reach new heights of optimization. For example, Black & Decker enhanced labor efficiency by 10% and equipment effectiveness by 24% at its plant by implementing a real-time location system.
The prevalence of IoT on the factory floor is only set to grow. Zebra Technologies reports that 62% of manufacturers surveyed expect benefits in automation and control processes from enabling IoT technologies.
Manufacturers that fail to join the revolution will miss out on a massive source of competitive edge, but adopting these new technologies is not without its challenges. To make the most of Manufacturing 4.0, businesses will need to pursue a fully connected digital ecosystem that eliminates bottlenecks and links previously independent silos. As a global content partner that specializes in the manufacturing sector, we’ve seen our fair share of smart factory implementations – so here we’ll share what we’ve learned, and explore the implications that Manufacturing 4.0 has for localization.
Key considerations when adopting an IoT system
Implementing IoT and IIoT systems can be complex tasks. Taking full advantage of the technologies often requires fundamental changes throughout an organization. If you’re still in the early stages of your Industry 4.0 journey, we suggest keeping the following considerations in mind:
- Security: A digital ecosystem is an entire infrastructure of connected devices that need to be secure. Organizations need to have contingencies in place to handle new equipment, security breaches, and the evolution of their IoT network.
- Legacy issues: One of the advantages of IoT is that it helps businesses pinpoint areas of improvement, such as legacy data management systems that hoard data in silos instead of sharing them across the network. It’s easier to solve a problem at the start of the process, even if the solution is a complete overhaul of an ancient system.
- Workforce drain: Implementing Manufacturing 4.0 is tough, as a lot of legacy systems are linked to proprietary networks and need to be brought together into a cohesive network. A business-wide system upgrade will also have an effect on productivity, and staff might need additional training to use the network properly. This is why it’s imperative to look for a system that’s easy to integrate; one that provides real-time connectivity so that teething issues are easy to identify and solve early on.
- Budget: The integration of a completely new system comes with costs. As the IoT industry is still in its infancy, determining ROI can be difficult. Immediate returns might be limited while you overcome teething issues, but long-term benefits are likely to be tremendous.
The impact on localization
Industry 4.0 is going to change product development across the board. As product release cycles shorten, localization processes will need to become more agile and proactive to keep up.
Today’s connected machines frequently receive software updates even after they are deployed. This means that the human-machine interfaces (HMIs) that operators use to control and oversee equipment also require content and localization updates. Similarly, user manuals are no longer set in stone when they are shipped with a machine. Manufacturers will need to adapt to a more dynamic content strategy and be prepared to deliver numerous, small updates over time.
We also recommend that businesses start to think more digitally. Online help pages, how-to tutorial videos, and even virtual reality training tools are emerging as excellent ways to augment traditional support content. And since digital resources are far easier to update, they naturally align with an agile approach.
Perhaps the greatest barrier to effective content creation and localization in an IoT-enabled environment is a siloed organizational structure. Data from IoT systems will be used in a variety of ways by different departments, so content will become more connected. To ensure that people get the data and information they need in a way they can understand and use, clarity and consistency are key – and without inter-departmental collaboration, that kind of consistency is impossible to achieve.
Don’t let localization be an afterthought
In the midst of a major IoT implementation, it’s easy to overlook localization – but optimizing your global content strategy early will pay dividends in the long-run. To take the weight off your shoulders, consider consulting your global content partner. At Rubric, we have the skills and resources to analyze your business processes and help you redesign your localization approach to align with your new manufacturing technologies. Get in touch!
Do you want to learn how business transformations could affect your localization process?
In our guide Best Practices for Business Transformations you will learn how to make the most of your translated content in times of change.